It's hard to believe it's been 35 years since the Rhodes factory shut its doors for good. Since then, Rhodes piano has gone from a down-and-out heavyweight junked for parts and sold at yard sales for pennies on the dollar to a true comeback kid!
Today Rhodes Pianos are on top as the reigning king of highly collectible and sought-after electric pianos. And there’s no doubt that this time they are here to stay.
Harold Rhodes’ piano changed the sound of music forever with its smooth bell-like tone and harmonic characteristics that let it blend in with and nurture just about any musical style with subtle grace while also affording the opportunity to stand out and demand attention. This range makes it an obvious choice for gigging and studio piano players alike. But it's not just the sound alone that makes the Rhodes such a mainstay in music. It's also the genius of its design. The simple action is something that even the novice player could maintain without formal training.
To celebrate the venerable Rhodes, let’s take a look back at what it was like in the factory all those years ago through the memories of Rhodes factory designers Steve Woodyard and Mike Peterson!
Beginnings
Hey Steve and Mike! Thanks so much for joining us. To start, tell us what year did you start with Fender and what was your official role?
SW: I started at Fender in Aug 1966 as a Guitar Technician. I went to school taking electronics and math. After a couple of years, I started to work in many of the Fender departments. In 1970, I transferred into the factory service department as a Senior Electronics Technician. In 1971, the Rhodes tech quit and I was given the responsibility of servicing the Rhodes. Harold came to my cubicle every week for a year, to train me. I didn’t start on the production of pianos until the 1980’s but I became a part of R&D as an assistant to Horst Absmann about 1979. Mike Peterson came on a couple years later to join the team.
MP: I joined Fender, Rogers, Rhodes in January, 1982. I had been working with Paul Rivera since 1976, building custom amplifier cabinets and pedalboard enclosures in my cabinet shop. When he was hired as marketing director for Fender amplifiers, he introduced me to Harold and the rest of the Rhodes staff
How long did you guys work at Fender?
SW: When I was laid off in Sept 1984, I had been with Fender for 18 years. During my time I had developed highly sensitive touch and hearing abilities, which helped me design and troubleshoot new ideas for new models.
MP: January 1982 To March 1985
And do you recall how many departments there were in the piano division?
SW: There was only one department and one piano line.
MP: There was R&D, Manufacturing and Marketing. Rhodes R&D consisted of Harold, Steve and me. Paul Sharp worked with us for a while on synthesizer projects. Mike Antill, Paul Gagon and Bob Haigler worked on electronic projects, both for Rhodes and on other Fender projects. After the ARP acquisition, a few of the ARP guys worked with us for the Rhodes/Chroma project, the Rhodes electronic piano and the Polaris synthesizer.
Horst Absmann ran all of manufacturing. Dwight Doerr ran the Rhodes line. The woodshop made the wood cases on the same line as Fender amplifier cases. The company had its own metal stamping facility, with a tool and die shop. Most of the metal parts were stamped in house. Tines, tone blocks, pickups, leg hardware grommets, hammer tips, keybeds, keys, hammers, hammer combs and other various parts were made by vendors. Harps were drilled and assembled in Ensenada Mexico. Final assembly and tuning was done in Fullerton.
John Shykun was marketing director. He was a brilliant musician who could make any instrument sound good. Steve Grom started in QC, but was later moved to marketing director when John left to work at Kurzweil.
Rhodes shared purchasing, drafting, accounting, warehouse and administration with the rest of Fender.
So what was a day in the life like at the Rhodes factory?
SW: I did customer service interaction while doing 1-2 pianos a day and 1-2 amplifier repairs per day.
MP: I actually had an office, with a door. Some days, I would close the door and think. My favorite time was in the model shop making parts. On my first day, I was introduced to the guys in the shop. They introduced themselves, and said that they would be making my parts. I said no, I make my own parts. In some shops, this would have been a problem, but they welcomed me, and we became friends
I made prototype hammers out of production hammers, cut up on the band saw, and glued together with super glue. I'm thankful to the guitar guys who showed me the baking soda and super glue trick. The prototype hammer was installed in a one-key model, and we all played it, for hours. It takes a long time to assess the feel of a piano action when you only have one key. Here is where Steve and Harold were particularly valuable. They had played and adjusted hundreds, maybe thousands of pianos, and had a highly developed critical touch.
Sometimes I visited the production line to watch the workers. I strongly believe that all engineers need to understand the production line. Sometimes I visited the machine shop and talked about tools, dies and fixtures. This often resulted in an argument. I wasn't shy about expressing strong opinions, and Horst angrily threatened to have me fired more than once. On other days, I visited him in his office and we had a friendly discussion.
The best part was working with Harold! I loved the guy! When I worked with him, he was 73, but he acted like an excited, passionate young guy. His energy inspired me! It was easy to see how much he loved his piano. But there were also times that he angrily threatened to have me fired.
Collaborations usually worked in one of two ways. In early stages, we sat in a room together and discussed problems and potential solutions. Harold was invaluable in describing the history of each part, and reminding us what ideas has already been tried years ago, and what the result was.
The other way we collaborated was with prototypes. I would go out in the shop and make a part; then bring it in for Harold and Steve to evaluate. As I worked on the project, my evaluation skills improved, but they were no match for the experience of Harold and Steve.
Was there someone that played each piano and signed off on it or sent it back for more work? On some pianos from the early years 1971/72 there are harp stampings by quality control personnel such as “Buz Watson” and “B. Kehoe”.
MP: The final assemblers kind of played them a bit to assess basic functionality, with a time limit. There was no "send it back". The testers and adjusters replaced whatever parts needed replacing, doing their best within the time allotted, to make a piano that sounded good.
I don't remember the names Buz Watson or B. Kehoe, before my time.
SW: There were two inspectors in the early years, Buzz Watson and Bob Kehoe. They tested and offered a pass or return back to the line for rework.
Factory Output
Do you recall how many pianos were made a year at the factory on average? Do you find Harold’s estimate of 250K pianos made over the entire run reasonable?
SW: In its best years the Rhodes output was 16,500 pianos (73, & 88 Stage and Suitcase versions).
MP: I kinda remember that the run of Mark V was 2500 units.
How were pianos tuned and voiced in the factory? I assume harps were pre-tuned on a bench but then someone had to final tune and voice the piano and set strike line and escapement when the piano was set up. Or was this not the case and it was all done by dimensional standards?
SW: Horst developed the modular concept using preset tapped holes. This was the beginning of the aluminum action rail and side supports era. Up until that time the action rail and support blocks were made out of wood and the strike line and escapement were set during the production process by an assembly technician.
With the production moving to a modular system, piano output at its height multiplied to over 60 pianos a day. Can you offer insight to what it was like?
MP: I watched the process once or twice, but didn't have the expert insight to understand all of the subtlety of what was going on. First thing was to level the keyboard, using paper shims. Then, they adjusted the tines and pickups, mostly listening for uniform volume. Any really horrible sounding tines were replaced, but the level of criticism was dictated by schedule. The piano was tuned with a strobe tuner and played. It was usually played in the mid-range of volume, not extremely soft or extremely hard. Before the Mark V restored proper hammer throw, the plastic key versions with reduced throw didn't have a very good loud sound or "bark".
The assembly line was made of steel rollers. The case was put on the rollers and parts were added, then it was pushed to the next station. The last station was a kind of sound-isolated booth, where the piano was tuned and adjusted.
What were the obvious differences in how pianos were built at the factory in the early days compared to the later? Meaning what kind of things originally did you do that later were outsourced or done differently?
SW: Staffing changed and got smaller as product sub-assemblies were outsourced to Ensenada Mexico. Rhodes no longer did harp woodwork or assembled tines, pickups and tone bars in-house. In Mexico, you had all new people learning the ins and outs and being faced with the learning curve of the piano, this added problems. Prior to Mexico if a tine was bad the technician could just go get another one and install it. Now, all the parts were in Mexico, so the tech had little fix opportunities to him. Bend a screw, add a spring, and nudge it here and there. Adding another spring to the tone bar helped in most cases because the grommet was new and could still isolate the tone bars, 10 years later no such luck due to squashed grommets.
MP: Many of the parts that were made by vendors didn’t have complete, detailed documentation. The design, tooling and manufacturing process was created and refined by Harold and the shop owner or master craftsman. The drafting department often simply drew a picture of the part, leaving out many of the critical details. This caused a lot of trouble when purchasing decided to switch vendors.
Did they assemble harps completely in Mexico? Including pickups, tines to tone bars, wiring and assembling the frame? There are stories of finding harps being drilled on uneven dirt floors in Mexico? What are your recollections?
SW: The pickup rail was completed at Turbo Jet, CA. and then sent to Mexico; all other harp parts were assembled in Mexico.
Where were all of the piano cabinets made and covered?
SW: The cabinets were made and tolex was applied in Fullerton CA.
MP: In the Fender woodshop, on the same line that made the amplifier cabinets. The protective steel corners were made in the Fender stamping shop. I’m not sure if the hinges and handles were made in the shop, but I kinda remember that they were.
Do you remember if Rhodes pressed tines into the blocks at the factory or were they delivered pre-assembled?
MP: I think this production was moved to Mexico some time before I joined the company. What I do remember is discussions about the precision of each part. As part of their investigation, Harold and Steve carefully examined a batch of bad tines and compared them to the good ones.
Also, the tone blocks were made from leadloy (steel with added lead) that ran through the screw machine faster. We discussed replacing this with a better alloy, but were never able to get them produced. Once the problems were understood, Harold went to management to demand a fix. Sometimes he succeeded.
Was there a line of workers who just cut tines all day long to length?
MP: I never saw this part of production; again it was probably done in Mexico. If I had to guess, I would speculate that they lined up hundreds on a saw table and gang cut them. I would also speculate that this wasn't done with a precision fixture.
Speaking of tines, what was the protocol for tine replacement with respect to QC?
SW: All purchased parts went through receiving inspection and were inspected against a production drawing. Tine failure was normally due to poor fit in the tine generator hole or mis-dimensioned parts that had been accepted by purchasing(Ex: tines that had ¼ in taper vs ½ in taper). Final inspection changed out the bad part.
MP: I never studied production enough to know this. What I do know, is that production workers had a very limited time to touch each piano. If I had to guess, I would say that they tuned it, and if every note was close enough to sounding good, it was shipped. The testers were good, but limited in time. When Steve set one up, he took a lot more time and was a lot more critical.
Do you know why different tine manufacturers were utilized, it seems like Torrington was the longest used manufacturer, why the switch?
SW: We went from Ray Mac centerless ground piano wire tines that would break in groups to swaged steel tines made by Torrington, then Singer and Shaller due to improving the reliability and avoiding breakage.
Purchase New Fender Rhodes Tines here
With so many physical changes to pianos over the years, what were the reasons behind those changes, was it mostly economical, to save money, or was there a desire to do better. I think both would be valid reasons and I am sure you had to compromise your ideas for financial realities.
SW: To improve production which ultimately saves time and money.
MP: A bit of both. The flat top cover was introduced in response to musicians stacking other keyboards on top of the Rhodes. The Mark III EK10, was an attempt to integrate an early polyphonic synthesizer with the Rhodes. The plastic key design was done for cost savings. When I joined Rhodes, my assignment was to help Harold with his offset key design, reduce cost, reduce weight and improve manufacturing consistency.
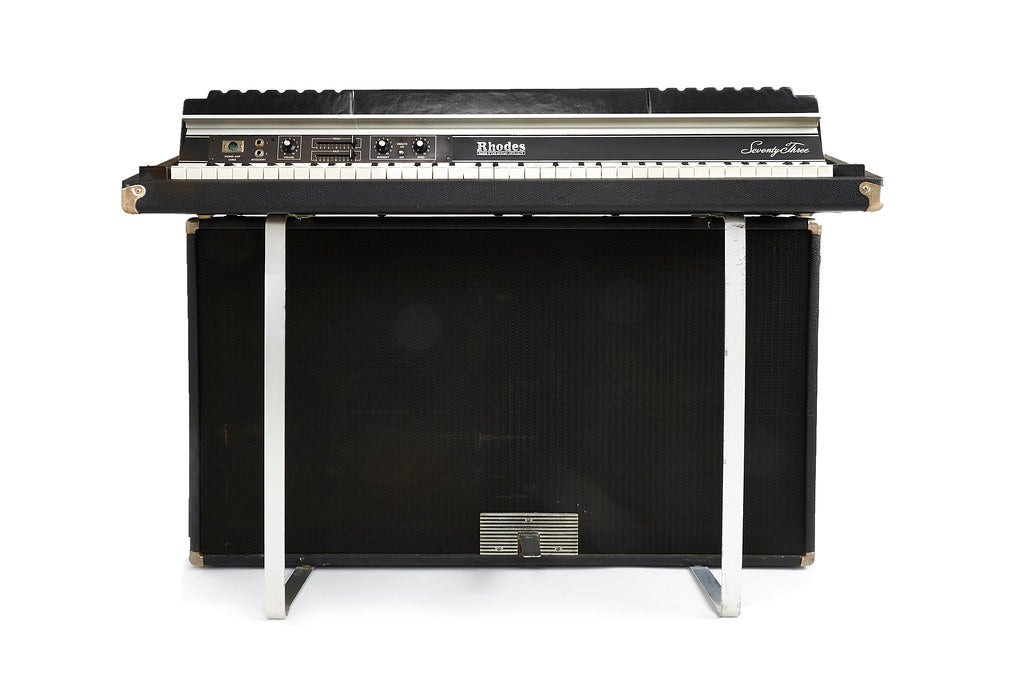
Rhodes Mark II Suitcase 73
Prior to the newly designed MKV, around 1982 Rhodes had changed to a plastic key bed for about 1-2 years. What was the reason for returning to the wooden key? Or better yet, why did they change to a plastic key?
SW: Horst‘s name is on the patents. He used the cabinet to give two feel ranges. At the time he felt the plastic designs were improvements.
MP: I don't remember who came up with the plastic key idea, but it was done to reduce cost, but whoever designed it had a limited understanding of plastic injection molding technology. I had long talks with Dan, the owner of the molding shop, as I designed keys for the offset-action Mark IV. Piano keys must be straight and stiff and dimensionally accurate. Making an 18 inch long injection molded piece of plastic straight and stiff is challenging. Dan worked hard on mold design and material selection. I think the keys ended up as glass filled polypropylene structural foam. The cycle time was slow, and yield was poor. Meanwhile, Wurlitzer was making perfectly good wooden key beds, using hundred-year-old technology. I never saw the numbers, but methinks the plastic key fiasco was a very expensive mistake.
Wurlitzer did make key beds for Rhodes. Was there any competition felt at Rhodes over the Wurlitzer electric piano or was it seen as totally different?
SW: No, they were two different animals. We did not feel we had any competition with Wurlitzer. We also didn’t feel any competition with Chuck Monte of Dyno My Piano.
Can you offer us any insight as to the many key pedestal changes over the years?
SW: Horst Absmann did not understand the bumps on the pedestals so he eliminated them. His sense of touch was not as acute as mine, I convinced Harold to put the bump back in. Harold could feel the difference immediately and easily. Harold recognized this and had me design the new hammer curves for the 54 stage and the Mk V. To achieve my desired feel on the MK V, I changed the dimensions of the balance rail location. I was looking for a 3/8 in key dip with a 2-1/2 in. hammer throw.
MP: I spent a lot of time analyzing and trying to understand the physics of the key/hammer/tine relationship, including the use of a 12,000 frame per second camera. For such a simple design, it has a lot of hidden complexity. All piano actions have a seemingly simple job. The player presses a key, which accelerates a hammer to hit a string or tine. The complexity arises after the strike, when the hammer must rebound without bouncing and striking multiple times. Traditional piano actions have a complex mechanism, involving moving jacks and backchecks. Harold’s insight was to invent a simplified action based on a curved sliding surface that combines acceleration and braking. Achieving a balance between feel, dynamics and lack of bounce was a challenge. Improving one of these things usually made the others worse.
Since the hammer and key meet on a curved surface, the geometry is nonlinear. This affects the feel and dynamics. The bump was an attempt to improve linearity as was my redesigned action concept for the Mark IV.
One of the biggest problems I have seen with making the Vintage Vibe Piano is dealing with vendors. Consistency and quality along with tolerances are big issues. Can you tell us what kind of experience you had with Vendors and how it affected production?
SW: Vendors can be a tremendous source of pain to a manufacturer. When relying on someone else to share your passion and expectations, you are setting yourself up for being let down. If you find the right vendor, they can be an integral part of your team and vision, if not, it can be a bad experience.
MP: The problem was not vendors in general, it was switching vendors. Harold worked closely with vendors to perfect the design and manufacturing process. Often the exact details existed only in the mind of the particular vendor engineer. The details were lost when purchasing switched vendors to cut costs. Also, some of the designs stretched the limits of vendor technology. The plastic hammers, combs and keys were very challenging to injection mold, and many injection molders would not even attempt to make them.
What were some of the struggles you and Harold dealt with in regards to improving or maintaining the piano's performance, setting aside financial reasons.
SW: The pianos were built to specifications, which were determined by fixtures and dimensions. Harold spent a lot time with the president, Bill Shultz, complaining about problems they were finding. The early pianos had parts design problems that needed to be rectified. When the vendor worked with us to develop a part there were little problems. When purchasing forced us to use a different or less expensive vendor there were lots of problems.
Another small issue was Delco who made the transistors for the Peterson amplifiers told us they were discontinuing the DTG-110B germanium transistors. Our in-house engineer Bob Haigler designed a new more reliable amplifier and pre amp. Unfortunately, the popular stereo vibrato had problems due to the LDR/LED part used to turn the vibrato signal on and off. It did not mimic the smooth rise and fall time of the incandescent bulb, it caused a more definite pulse missing the earlier smoothness, otherwise the Haigler was superior.
MP: Engineering and manufacturing are a series of finely tuned balances and tradeoffs. If you optimize for one thing, other things often suffer. A prime example is hammer throw. Longer throw improves dynamics and sound but results in more broken tines. As part of our R&D efforts, we tried putting a Rhodes harp on a grand piano action. It sounded great but tines didn’t last very long at all.
The Rhodes piano has a lot of parts. Even if we were able to invent the perfect design, it would not be economical to manufacture them perfectly using the tools and machines of the time. The music biz had a lot of middlemen making a profit, so manufacturing costs were forced to be low.
It is interesting to know that in order to build pianos and earn profits the pianos have to be built to dimensional standards. Meaning there was no real time spent articulating the pianos to optimal specifications; yet this worked. Were there customer complaints about pianos not performing well? Customers spent good money; I am sure there was an expectation of playability? Was it expected or understood that the dealer tuned up the piano prior to selling to the customer?
SW: The pianos were produced to be ready out of the box without dealer articulation or modification.
MP: During our R&D work, we discovered that some dimensions were very critical. Unfortunately, the shop was unable to hold the tolerances we asked for. We were constantly forced to loosen our tolerances in order to avoid scrapping a batch of out of tolerance parts. Remember, this was the days before CNC machines. We wanted machine shop accuracy. The woodworkers delivered woodshop accuracy.
The lack of quality control lead to inconsistency. Some pianos were excellent, some very poor. Some could be improved by the individual attention of a master tuner like Steve, some were simply too far out of spec.
Was this how Dyno My Piano came to be, in reaction from customers wanting more from their Rhodes pianos?
SW: Dyno My Piano was not a factor to Rhodes in how we made pianos. Customers wanted an additional amp for the Rhodes. Dyno My Piano gave them one
MP: I never met Chuck and we didn’t have any of his designs in the R&D lab.
What were some of the biggest concerns from customers in your time? Weight, size, action or something else?
SW: Weight and performance were the main concerns. Horst and Harold were very responsive to the needs of the market and our customers.
MP: Weight, size and consistency were the main problems we worked on. We also worked on sound and dynamic range. Getting the action to play a soft note and a loud note, without bounce and restrike, was our biggest challenge.
It seems as if there was a constant power struggle between corporate profits and making a great piano the best way you and Harold knew how. These two ideas often were at odds with each other. How did you and Harold deal with this problem?
SW: I was not involved but Harold was very frustrated when his vision was obstructed by financial constraints.
MP: There were many factors involved. While the management annoyed us by switching vendors and moving production to Mexico, they also funded the R&D department. I had the strong support of Roger Cox, VP of R&D. My R&D related requests were never denied.
We also struggled against physics and manufacturing technology. The Rhodes is a complex balance of a lot of things. As hard as we tried, we never fully understood all of the details of the physics. We didn’t know if it was possible to perfect the piano, but we did our best to improve it. We accepted the physics and manufacturing challenges as part of the life of an engineer, but we were sometimes surprised and angered by the stupid decisions of management.
Working with Harold

Harold in Factory, Fullerton, CA 1982
What was Harold like to work with on a daily basis, give us an insight to his mindset?
SW: Working with Harold was great, but we learned to keep an eye on where he put his sweater and keys down.
SW: For Example, one day Bob Haigler and I were talking at a NAMM trade show when Harold walked up and asked us what we were talking about. I replied that we were sharing Harold stories and I had just related the one where Harold had driven to LAX parked his car and flew to the east coast. He then returned to LAX and took a taxi home. Harold said he had a better one and told us how he had driven to Portland, OR and then flew home.
At his memorial service I told this story and his daughter Carol told me about the time they'd bought pocket knives with “LOST BY HAROLD RHODES” engraved on them and that they weren’t surprised when Stevie Wonder returned one to Harold.
SW: Harold was unique. He had the ability for deep concentration. He loved Lincolns. He bought a MK I and named the piano after it.
I tell people that a Rhodes Piano has 2 owners, the person who purchased it and Harold. He feels responsible for every one out there
MP: He was an inspiration and a truly wonderful guy. I loved working with him and we worked well together. I respected him as the original inventor, he respected me as a talented, creative outsider with fresh ideas.
Did Harold ever personally build pianos later on, maybe for friends? The reason I ask is we have a 92-note piano that was made for Michel Legrand that was supposedly built for him, by Harold. It’s an interesting piano, one of a kind I am sure. The harp is all one piece as well as the case with original tolex, but the key bed is made from 2 key beds and the front name rail is from an 88 note but drilled off center to accommodate the scale. The lid is grafted together from two separate lids. Does this sound like something Harold would have done, maybe in his garage?
SW: Harold did make a couple of custom Pianos including one for Michel Legrand. He made some in the early years but later his garage housed his fire engine.
What was your favorite era or year of piano and why?
SW: I do not have a favorite era but one of my favorite pianos is a 1971.
MP: All of us agreed that the Mark V was the best Rhodes ever.
Did you realize while you worked and designed at Rhodes that you were a part of history in the making?
SW: I did not have a clue as to how the future would see this piano.
MP: As a guy who started working with bands in jr high school, working with one of the legends of the musical instrument biz was exciting.
What was going on, project wise, at the time you found out the factory was closing?
MP: The Mark IV project had been cancelled. We were producing the one and only run of Mark V pianos. The attitude of the production shop was depressing, and it made me angry. I insisted that fixtures be improved to meet our design specs. They answered: “Why? After this run, it's all over.”
One of a Kind - Mark V Stage 88
Rhodes Mark Five 88 Note Prototype - The Greatest Piano That Never Was
Closing up Shop
Did you have a sense the factory closing was eminent? Was there a race to save it design wise, so to speak?
MP: More than a sense, the production worker's union demanded more money. Management told them that if they voted to strike, the factory would be closed. They voted to strike.
At the same time, we could all clearly see the future. It was electronic keyboards and samplers. Our marketing director, John Shykun left the company to work for Kurzweil, which had the most exciting product at the time.
Was everyone laid off at the same time?
MP: The management intended to keep the guitar and amp business going, so some of the key people stayed. My friend and marketing director for amplifiers, Paul Rivera, left to start his own company. Rhodes and Rogers were killed. My boss asked me if I could see any place in the new company that I could fit. I answered no.
Were you there till the end?
MP: Fairly close, but not quite: after I agreed that my future was elsewhere, my boss (and friend) let me use the model shop to make a really nice computer desk.
There must have been parts and pianos all over the factory, this must have been surreal. Did you feel hollow at the thought of your hard work and designs being left behind unfulfilled of their potential?
MP: I looked to the future, to my next adventure. I could see the larger forces of history at play, and realized that there was nothing I could do to change it. I take pride in always finishing projects. I'm sad and disappointed that I never got a chance to finish the Mark IV project
What happened to the factory, once you were laid off, did it sit unused or did CBS repurpose the space immediately?
SW: CBS sold it to a management company and everything moved out. The factory shut down and the guitar production moved to Corona CA.
MP: The Fullerton factory was sold and later demolished. An industrial park was built on the land.
Knowing the decision to close the factory came from corporate, this must have really stuck a knife in the hearts of Harold, Steve and everyone else who was part of the evolution and design of the Rhodes piano. What was Harold’s mood like if you can recall?
MP: One of my favorite things about Harold was his optimism. He inspired us all. It was very sad to see him in the last days. We all knew that electronic keyboards like the DX7 and Kurzweil were seen as the future. When that was combined with the factory closing, Harold said: “Maybe it's time to retire the piano.” This made me sad to hear.
In the end, American manufacturing was against the ropes with the imported Asian digital pianos and synthesizers coming in. How did you process the ideas you had for the electric piano after leaving the factory?
MP: I moved on to other things, and left the music biz behind. My next adventure was working with a world famous eye surgeon to develop a revolutionary new machine for eye surgery, followed by a really exciting, productive and fun time at Walt Disney Imagineering, and many more adventures, over a long career.
Did your design ideas haunt you knowing you had no way to implement them any longer or were you able to disconnect and not look back by putting your creativity in your next endeavor?
MP: A bit, but my adventure continued in different directions. The piano was Harold's life work and a big part of Steve's life. For me, it was one of many adventures in a life of inventing and engineering. It was one of the best times in my life, but as time passed, there were many other great projects and adventures.
I respect the piano as one of the great instruments of all time, and I'm proud to have contributed a bit to its development.
I'm a bit sad that I didn't get the chance to finish my project, but that's the life of an R&D engineer. My life has been a series of projects and adventures, some successful, some partially successful and some not so successful. I look forward to the next adventure. I'm not done yet.
Do you own a Rhodes today that perhaps you built or had a hand in building?
MP: One of the saddest failures in my life is that I never learned to play the piano. I spent hours in lessons and practice, but never achieved much. Musical talent is real; I don't have it. I do have a bit of composition talent, and have made a lot of music using computers and virtual instruments.
Despite the challenges, frustrations and failures, it was one of the best times of my life. I loved being part of the music world. I loved working with Harold, Steve and the other folks at Fender, Rogers, Rhodes. Many of the other employees were very talented musicians. I owned a small recording studio, and many of them made great music there.
All of the music recorded in the studio is available on my website, loudroundrecords.com. Years after I left, I wrote an article about my time at Rhodes, it’s also available on the website.
Interview by Chris Carroll
Chris Carroll is the owner of Vintage Vibe Electric Piano Co. Vintage Vibe